Advantages of BLDC Motor Controllers: A Comparison with Conventional DC Alternatives
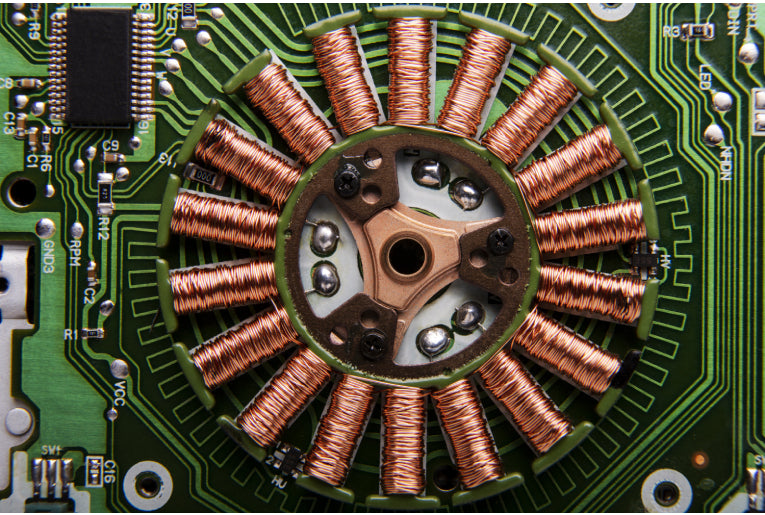
In the world of electric motors, advancements in technology have paved the way for more efficient and precise control systems. Among these innovations, Brushless DC (BLDC) motors have gained prominence for their superior performance in various applications. BLDC motor controllers, specifically designed for BLDC motors, have become the go-to choice for many industries due to their numerous advantages over conventional DC motor control systems. In this article, we will explore the key advantages of BLDC motor controllers, with a focus on their use in field-oriented control.
Understanding BLDC Motor Control Systems
Before diving into the advantages of BLDC motor controllers, it's essential to grasp the basics of BLDC motors and their control systems. Unlike conventional DC motors, BLDC motors do not rely on brushes for commutation. Instead, they use a permanent magnet rotor and electronic commutation to achieve rotation. To control the speed and direction of a BLDC motor effectively, a specialized BLDC motor controller is employed.
Field-oriented control, also known as vector control, is a precise method of controlling BLDC motors. It involves aligning the magnetic field produced by the stator with the rotor's magnetic field, allowing for smooth and efficient motor operation. This advanced control technique is one of the main reasons why BLDC motor controllers outperform conventional DC motor control systems.
Advantages of BLDC Motor Controllers
- Efficiency: BLDC motor controllers are known for their remarkable efficiency. Field-oriented control allows for precise control of the motor's magnetic field, reducing energy losses and maximizing efficiency. This is particularly crucial in applications where energy conservation is a primary concern, such as electric vehicles and industrial machinery.
- Smooth and Precise Control: BLDC motor controllers offer exceptionally smooth and precise control over motor speed and torque. Field-oriented control enables seamless transitions between different operating conditions, resulting in reduced vibrations and noise. This makes BLDC motors ideal for applications where precision is paramount, such as robotics and medical equipment.
- Extended Lifespan: The absence of brushes in BLDC motors eliminates one of the primary sources of wear and tear in conventional DC motors. As a result, BLDC motors and their controllers have a longer lifespan and require less maintenance. This reliability is especially valuable in applications where downtime is costly, such as in manufacturing processes.
- Higher Power Density: BLDC motors can deliver higher power densities than their brushed counterparts. This means they can generate more power for a given size and weight. As a result, BLDC motor controllers are favored in applications where space and weight constraints are critical, such as aerospace and automotive systems.
- Regenerative Braking: BLDC motor controllers can implement regenerative braking, which converts kinetic energy back into electrical energy when the motor is decelerating. This energy can be stored or fed back into the power supply, further enhancing energy efficiency and reducing operating costs in electric vehicles and other applications.
- Improved Thermal Management: BLDC motor controllers can better manage heat generated during operation. Field-oriented control allows for more precise control over the motor's power output, reducing heat generation. Additionally, the elimination of brushes reduces friction, which can also contribute to lower operating temperatures.
- Variable Speed Operation: BLDC motor controllers excel in applications requiring variable speed operation. Whether it's a fan adjusting its speed based on temperature or an electric vehicle smoothly accelerating from a standstill, BLDC motor controllers provide precise control over a wide range of speeds.
- Reduced Electromagnetic Interference (EMI): BLDC motors produce less electromagnetic interference compared to brushed motors. This makes them suitable for applications where EMI needs to be minimized, such as in medical devices and sensitive electronic equipment.
- Digital Communication: BLDC motor controllers often feature digital communication interfaces like CAN (Controller Area Network) or UART (Universal Asynchronous Receiver-Transmitter). This allows for seamless integration with microcontrollers and programmable logic controllers (PLCs), enabling advanced control and monitoring capabilities.
- Adaptive Control Algorithms: Some BLDC motor controllers incorporate adaptive control algorithms that can optimize motor performance based on real-time conditions. These algorithms can adjust parameters like current limits and voltage levels to maximize efficiency and torque output.
Comparison with Conventional DC Alternatives
To appreciate the advantages of BLDC motor controllers fully, it's essential to compare them with conventional DC motor control systems, which include brushed DC motors and their associated controllers. Here's a brief comparison:
- Efficiency: BLDC motor controllers are more efficient due to their precise control mechanisms. Brushed DC motors suffer from brush wear, leading to energy losses and reduced efficiency over time.
- Maintenance: BLDC motors have longer lifespans and require less maintenance than brushed DC motors, which need periodic brush replacement.
- Noise and Vibration: BLDC motors are quieter and produce fewer vibrations due to their smoother operation compared to brushed DC motors.
- Control Precision: BLDC motor controllers offer superior control precision, making them suitable for applications requiring high levels of accuracy.
- Size and Weight: BLDC motors can deliver higher power densities, making them smaller and lighter for a given power output compared to brushed DC motors.
- Regenerative Braking: BLDC motor controllers can implement regenerative braking, saving energy in certain applications, while brushed DC motors cannot.
- EMI: BLDC motors produce less electromagnetic interference, making them preferable in applications where EMI needs to be minimized.
In summary, BLDC motor controllers, especially when used in conjunction with field-oriented control, offer numerous advantages over conventional DC motor control systems. Their efficiency, precision, longevity, and adaptability make them the preferred choice in a wide range of applications, from industrial automation to electric vehicles and beyond. As technology continues to evolve, BLDC motor controllers are likely to play an increasingly vital role in the development of more efficient and sustainable systems across various industries.
Leave a comment (all fields required)
Comments will be approved before showing up.