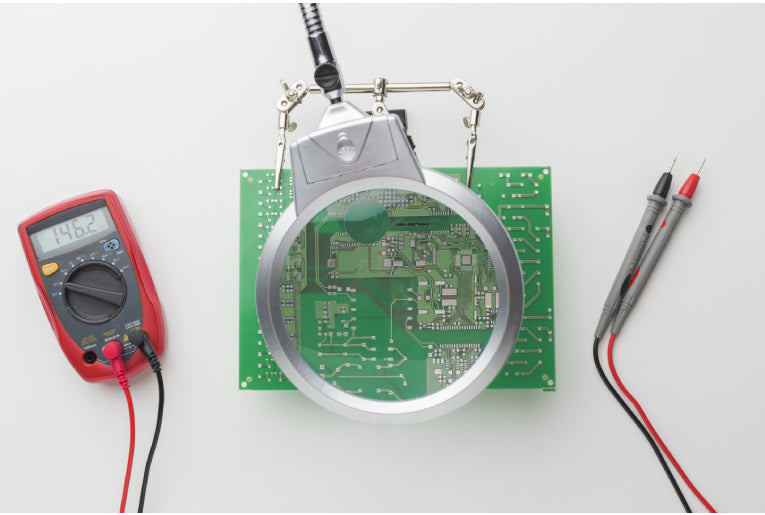
Motor controllers play a crucial function in many modern-day applications that regulate the electric motors. There are many kinds of electric motors that are available, brushesless DC (BLDC) motors excel, and their performance is largely dependent on the longevity and efficiency of the motor controllers made with brushless technology. In this thorough and in-depth piece, we'll dive deeply into the art of developing and constructing motor controllers that last in the long run, with particular focus on motor controllers that are brushless (BLDC motor controllers). The article will examine the most important elements, design concepts production processes, as well as the importance of longevity for these vital gadgets.
Understanding Brushless Motor Controllers
Before we get into the intricacies of developing and making motor controllers let's lay the foundation of the fundamental concepts. Brushless motor controllers also called BLDC motor controllers are complex electronic devices used to control the direction and speed of DC motors that are brushless. They are unnoticed stars in a myriad of different applications that include electric vehicles, industrial machinery electronic consumer products, as well as robotics.
Key Components of a BLDC Motor Controller
An BLDC motor controller an intricate system that consists of several essential components that each play a distinct purpose in maintaining the motor's operation is smooth:
- Microcontroller Unit (MCU):
In the center of every BLDC motor controller lies the microcontroller device, which is which is a brain-sized device which is in charge of executing control algorithm as well as monitoring parameters of the motor as well as processing feedback signals from diverse sensors.
- Gate Drivers:
Gate drivers function as the nerve system for the controller. They send exact voltage signal to motor's power transistors. They determine the timing of switching these transistors which, in turn, determine the speed of the motor and its direction.
- Power Transistors:
The power transistors provide the force driving the action. These devices with high power function as electronic switches that regulate the flow of electricity across the motor's wires and by doing so, influencing the power supply to the motor.
- Sensors:
Sensors, like Hall effect sensors, or encoders are sensors for the motor's sensory organs offering vital information about the position of the motor and its speed. This is essential to allow the MCU in order to precisely control the operation of the motor.
- Power Supply:
A reliable and steady power source is the blood supply to the BLDC motor controller. It ensures continuous and reliable operations.
Design Principles for Endurance
With an in-depth understanding of elements, let's dive into the fundamental design concepts that are the basis for the lasting effectiveness that is the hallmark of BLDC motor controllers.
- Robust Circuit Design:
The base of a reliable BLDC motor controller is its circuit layout. Engineers need to pick components that will not only comply with the specifications of the industry, but are also capable of enduring the rigorous demands of the program. Solid circuits ensure long-term reliability.
In addition to this: The circuit design must also take into consideration factors such as electromagnetic interference (EMI) as well as electromagnetic compatibility (EMC) to avoid negative effects to the performance of the controller and the surrounding environment.
- Efficient Cooling Systems:
It is possible for overheating to be an invisible killer for motor controllers. In order to ensure longevity, the use of reliable cooling devices is crucial. Fans, heatsinks and liquid cooling units can help in dispersing heat while maintaining ideal operating temperatures.
Extending on this idea: Advanced thermal analysis and simulation software can assist in the design of better cooling systems. improving heat dispersal and decreasing the possibility of stressing on the components.
- Protection Mechanisms:
Incorporating robust security features is essential. They include protection against overvoltage and overcurrent, are the controller's defense system that protects against electrical problems that might harm the controller and the motor connected.
Further extending on this idea: Protection mechanisms can be extended beyond just electrical security to include fault detection as well as predictive maintenance functions which can improve overall reliability of the system.
- High-Quality Materials:
The materials that are used for the manufacture of motor controllers has a significant impact on its longevity. The best PCB substrates and connectors as well as other components minimize the chance to wear and tear with long periods of time.
Expanding on this point: Utilizing advanced materials, like ceramic substrates or high-temperature-resistant coatings, can further enhance the controller's resilience, particularly in harsh operating environments.
- EMC Considerations:
Electronic compatibility (EMC) isn't just an obligation of the regulatory system; it is essential to ensure that the control unit does not interfer with the other electronic components of the system or fall prey to interference from outside. A proper shielding and filtering system is crucial to ensure EMC conformance.
To expand on this idea: EMC testing and conformity should form an integral element of the controller's development and production process that focuses on reducing the emission of electromagnetic radiation and susceptibility.
Manufacturing Processes for Endurance
Making a sturdy BLDC motor controller but one aspect The manufacturing process is just as important in ensuring long-term durability and reliability. Explore the essential factors in manufacturing motor controllers that can last.
- Quality Control Procedures:
A rigorous quality control process is vital during manufacturing. This involves extensive testing of the individual parts assemblies, as well as extensive testing of the end product to detect imperfections and fix them.
Further extending on this idea: Implementing statistical process control (SPC) methods can assist keep track of and ensure the stability of manufacturing processes. This can help reduce variation and ensuring that each manufacturing unit is in compliance with the specifications for quality.
- Surface Mount Technology (SMT):
Surface Mount Technology (SMT) can be described as the very foundation of today's electronics manufacturing. It allows for precise positioning of components on PCBs. It also ensures secure connections, streamlined designs and overall strength.
To expand on this aspect: Fine-pitch SMT, which has smaller footprints of components as well as more dense components, calls for modern manufacturing equipment and procedures to produce the highest-quality and durable solder joints.
- Automated Assembly:
Automated assembly systems streamline the process of production increasing efficiency and consistency. Automatization reduces the chance of human error, resulting in more stable motor controllers.
Further extending on this idea: The integration of robots as well as smart manufacturing methods will increase efficiency of production whilst ensuring the highest quality levels and sturdiness.
- Environmental Testing:
Conducting extreme environmental tests is vital. The cycling of humidity and temperature along with vibration as well as shock tests can help determine possible weaknesses in the design and flaws which may only be apparent when the conditions are extreme.
Further extending on this idea: HALT (Highly Accelerated Life Testing) and HAS (Highly Accelerated Stress Screening) methods of testing can be used to model and identify potential failure mechanisms and ultimately increase the endurance of the controller.
- Traceability:
The process of establishing traceability within the production process isn't just a measure to ensure quality but rather a proactive strategy to make sure that any problems are quickly spotted and corrected, resulting in the same high-quality standards.
Extending on this concept: Advanced traceability systems using RFID (Radio-Frequency Identification) as well as IoT (Internet of Things) technology can give real-time insight into the manufacturing process and allow immediate corrections when there are deviations.
Importance of Endurance in Motor Controllers
The endurance of motor controllers goes well beyond just reliability. it has a direct impact on the longevity and performance of the whole device. It is important to understand the reasons why endurance is crucial:
- Extended Lifespan:
Motor controllers specifically designed for endurance greatly contribute to the longer longevity of the BLDC motors. This is crucial for applications in which frequent repairs can be costly, but can also disrupt operations.
Extending on this idea: Prolonging the lifespan of BLDC motors is not just a way to reduce the overall costs of ownership, but also reduces the environmental impact by reducing consumption.
- Improved Efficiency:
Efficiency and endurance are two of the most important aspects. A reliable controller for motors ensures that the motor is operating with maximum efficiency which means reducing energy usage as well as minimizing the amount of heat generated which could be harmful to components with sensitive parts.
Further extending this concept: The optimization of motor controller's efficiency could affect the efficiency of the entire system particularly in cases in which energy consumption is an essential element.
- Reduced Maintenance Costs:
Robust motor controllers are less prone to repairs and maintenance. This results in significant cost savings in the longer time, since maintenance costs as well as downtime is minimized.
To expand on this concept: Predictive maintenance techniques that are enabled by sophisticated sensors and data analytics will further cut down on the cost of maintenance by finding potential problems before they cause breakdown.
- Enhanced Safety:
It is a fundamental aspect of security. A motor controller with endurance is more likely to not malfunction unexpectedly, thus reducing the chance of accidents and destruction to equipment, and the most important thing is to ensure the safety of both their users.
Further extending on this idea: In safety-critical applications the use of redundant motor controllers can be used to give failure-over capability and improve overall system stability.
- Consistent Performance:
In the end, endurance is a guarantee that the motor controller has the same performance throughout its entire life. Its reliability translates into steady and stable operation. crucial in situations where stability and precision is crucial.
Extending on this concept: Advanced feedback control algorithms and adaptive tuning could increase the capability of the controller to provide consistent performance in various circumstances.
Key Takeaways
It is a summary of the process of developing and making motor controllers that last and last, particularly motor controllers that are brushless (BLDC motor controllers) is a complex procedure that requires careful analysis of design concepts, components and production techniques. For motor controllers to last:
- Choose a strong circuit which can stand up to the demands of your application as well as EMC aspects.
- Utilize efficient cooling methods to avoid overheating using advanced thermal analysis.
- Consider incorporating protection functions and advanced fault detection.
- Make use of high-end materials, such as the most advanced and durable materials designed for extreme environments.
- Accept quality control processes such as Automated assembly, SMT as well as modern tracking.
- Submit motor controllers to severe test in the laboratory, which includes HALT and the HASS.
Insuring that motor controllers last not only improves the efficiency and endurance of the equipment, it can also result in significant cost savings, enhanced reliability, and safety. whether powering electric cars or driving industrial machines or even enabling electronic devices for consumers robust motor controllers are the silent champions who assure the smooth running of modern technology. It's not just something to be desired, but it's necessity for motor controllers that last.
Leave a comment (all fields required)
Comments will be approved before showing up.