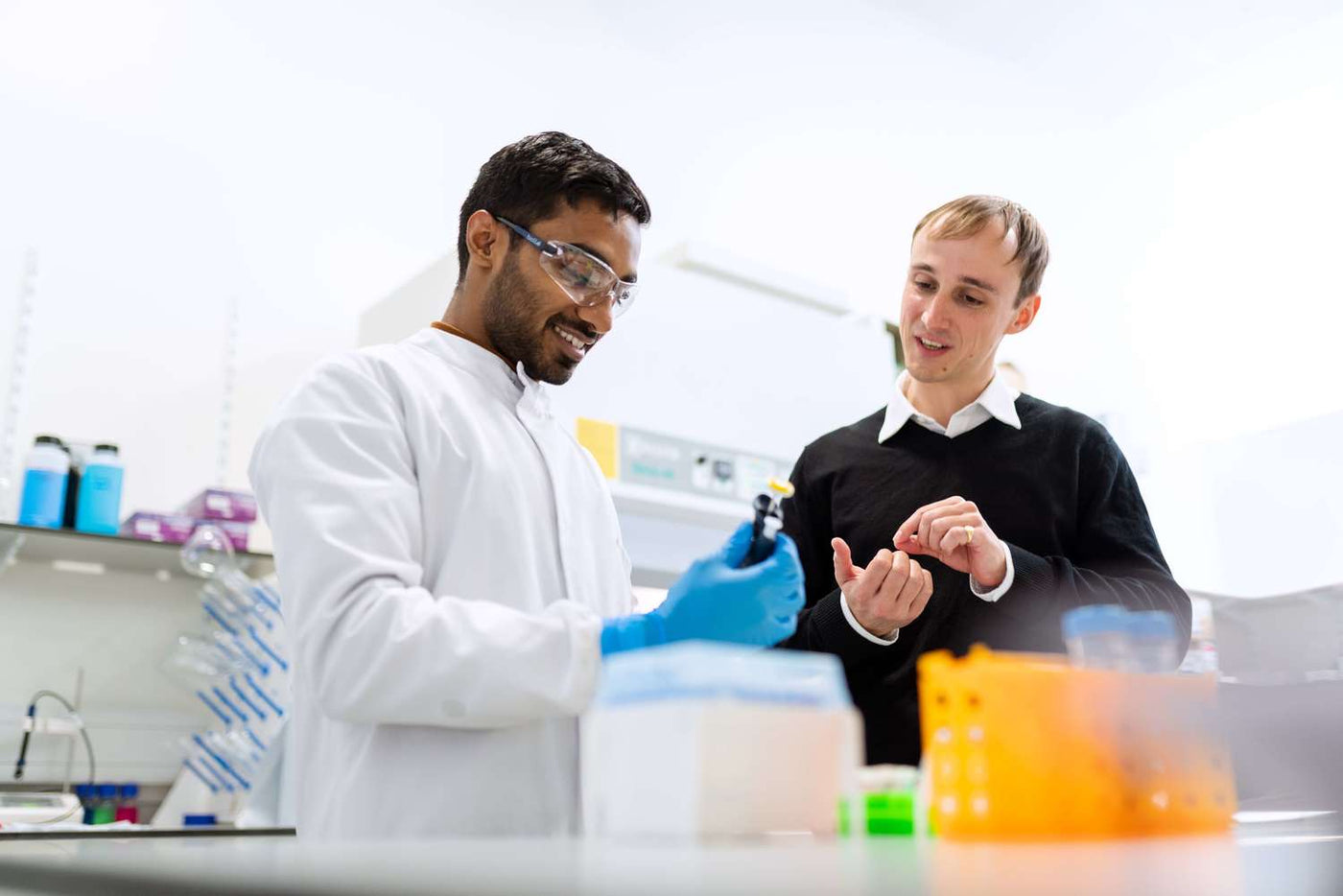
Finding medical equipment manufacturers, engineers, and production teams aligned to a standard product model enhances product quality by reducing production errors and increasing yield prices.
Manufacturers of medical devices face more significant obstacles than ever before in obtaining high-quality products so that the market can go faster, less expensive.
That is why it’s time for medical device companies to adopt a design approach to manufacturing where designers, engineering, and production teams are aligned with the same product model.
Medical Software Design
The experience of healthcare to digitization is accompanied by a significant quantity of revolutionary technologies, from IoT-related units to VR simulator systems.
Some have already carried out the scientific exercise have modified it for the better; others are beneath development.
Medical software program options take the leading role amongst the traits of digital transformation in healthcare. How to create a good scientific answer and advantage from it? Let's see!
Why Should You Build Healthcare Software?
Digital options make the scientific gadget greater personalized, turning it into any time, any-place, non-stop care. So, we are witnessing the introduction of a new commercial enterprise mannequin — a customer-centered digital healthcare ecosystem.
Medical Device Quality
Medical device companies that adopt a coherent and integrated production process — where CAD, FN / FEA, electricity, CAM, it's testing, quality management, work instructions, ERP, and software design (MES) are synced, Product descriptions of CAD programs that serve as intermediate product descriptions - they can increase their quality and design while cutting costs in three critical ways.
Fast-to-prototype time. Synchronizing the basis of various programs enables medical devicemanufacturers to reduce the time to do things more efficiently while enhancing product quality.
Where intermediate product models are embedded in CAD systems, it is a crucial definition of a reliable engineering and production product. Teams have the analytics, data, and information they need to take action in the language or dictionary they speak.
As a result, companies using this approach see an increase in new product launches with fewer design errors and prototypes while also preventing future production problems.
5 Things You Can Do Now to Improve Quality in Medical Product Development
Regulatory agencies regularly monitor manufacturers and manufacturers of medical products.
Unless they are accompanied by many demands on them, they cannot produce functional products.
Standards and regulatory bodies such as the FDA, ISO, and IEC may seem challenging in their implementation, but they must apply the highest and strongest standards when it comes to life-saving products.
1. Review process:
It sounds like an essential thing, but there needs to be one process that runs all product functions. It must consider all aspects of the product development and delivery and ensure that needs are established and met before allowing. It may be regarded as a work in progress, but it is a matter of quality in its context. Signing out is not as important as explaining and sticking to it to create a quality product. At each step in the process where this needs to be done tested and verified.
2. Audit procedures:
Maybe creativity is not enough, but it is a start point. The most important part of this step is to use the audit process to identify where the quality can be achieved and fix it immediately. That's all to help medical equipment manufacturers speed up the process of delivering their products through direct marketing. It is always known that there is a direct link between the time of detection of quality problems and the speed at which the product will pass legal inspection and be brought to market.
3. Feedback loops:
Quality is not a goal and has never been fully achieved. Each action in the product life cycle requires a new set of eyes to review and ensure quality.
The QMS can assist in establishing and pursuing a typical response among stakeholders and decision-makers, allowing for immediate action and immediate resolution of issues that may affect product development.
4. Content management:
Standard bodies and regulatory agencies will seek to review all aspects of product design.
If any documents are lost or deemed lost because they are not correctly aligned, it will become a red flag and may cause unnecessary delays in development.
Using QMS enables all documents to be stored, tagged, and resources where necessary to facilitate further development.
5. Corrective action:
CAPAs are designed to minimize malfunctioning processes and to address issues before completely disrupting projects. However, often the corrective action is not followed.
The QMS is essential because it helps establish the quality standards to be met and use the causes otherwise.
CAPAs are one of the most important time-saving features and resources for using QMS.
Leave a comment (all fields required)
Comments will be approved before showing up.