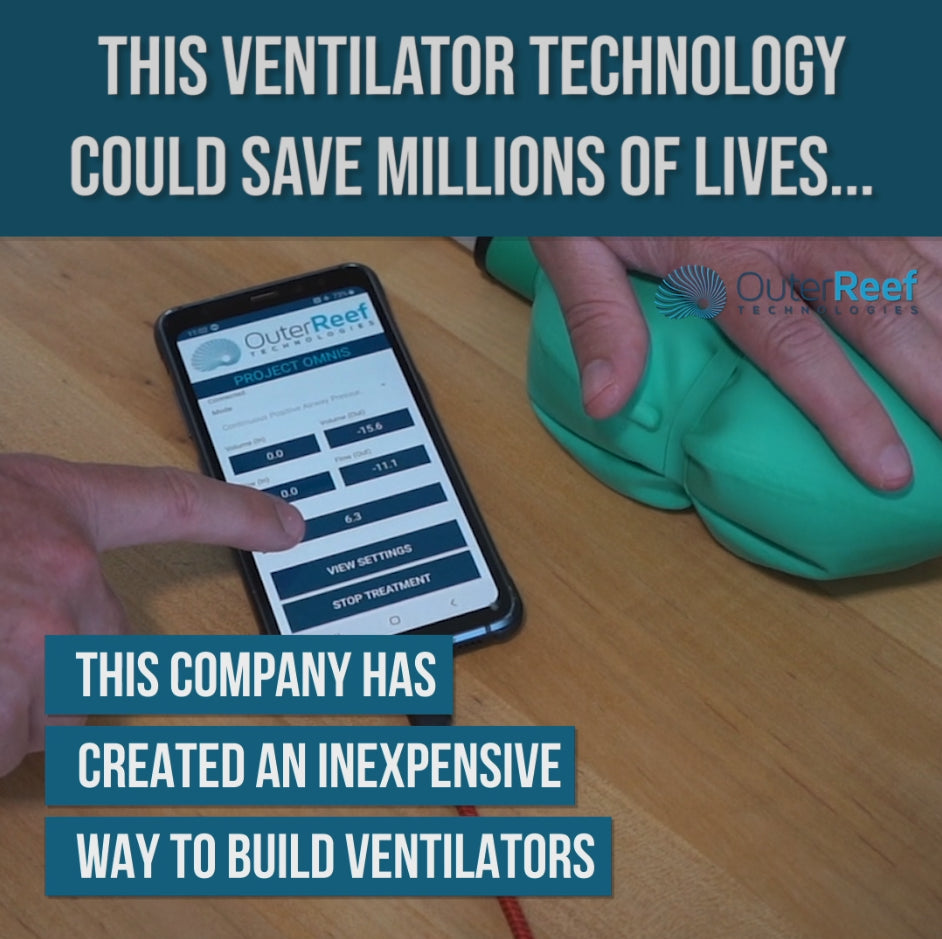
Due to COVID-19, more and more hospitals are short on Ventilators. In response to the global pandemic, many medical device manufacturers have been designing new ventilator designs across the world. Here we summarize some of the ventilator design lessons from Project Omnis and what we learned during their time-sensitive project.
Read on for some COVID-19 Ventilator design lessons that cover tactics and examples of summative research that went into adapting to the pandemic guidelines.
6 Must-Know COVID-19 Ventilator Design Lessons
From human challenges to working from home, and more, read on as we talk about some of the COVID-19 design lessons learned this year.
Challenges That Arise With Ventilator Design
While COVID-19 remains in progress, it limits teams from doing the usual preliminary analysis routine. That process normally involves collecting contextual analysis on-site through Key Opinion Leader (KOL) interviews, gathering and analyzing ergonomics, and understanding workflows. Typically these processes are done with analogous devices to develop the necessary workflows required to start a project.
Another challenge that comes is learning how mechanical ventilation works and appreciate the user interface requirements in a short amount of time to develop the appropriate interface components and ventilation parameter controls. In order to create a usable and successful product, you need to have an innate understanding of how that device works.
One challenge that the Emergency Ventilators Project faced was trying to take a large number of controls and indicators that would typically be used on separate screens into a single plane that would be easy for users to understand. Lastly, one of the COVID-19 ventilator design lessons is the lack of time to talk to people about this project. Typically, medical manufacturing projects are heavily supported with KOLs and small and medium-sized enterprises (SME) from some of our clients. It’s essential for projects like this to get as much input as possible before deciding what to do from a design perspective.
Ways That COVID Change The Way Tests Are Conducted
There are lots of ways that COVID changes the way that tests are conducted. One of the biggest challenges with COVID-19 is not being able to meet face to face with participants. Instead, they had to envision new ways to conduct formative testing. Instead of meeting at a physical test location, developers were forced to meet participants virtually through an online meeting room.
However, this type of testing proved useful. Not only does it remove the uneasy that participants feel with test personnel in the room, but it also more natural accommodated participants testing the graphical user interfaces. Online meetings shorten organizational times to arrange and execute studies, even though identifying potential user errors was harder to spot virtually. The capability to provide a rough prototype for participants to interact with physically has been removed because of COVID-19.
Though it was challenging to get user feedback, it wasn’t impossible. Typically design experts observe participants while they interact with the equipment, but this time, the only feedback is verbal, crafted from carefully asked questions.
Hurdles That Come With Working From Home
Another one of the COVID-19 ventilator design lessons is that working from home presents its own unique challenges. For example, teams don’t have the same tools and direct access to other team members as they usually do within the office. All the things that generally come easier at the office, like time management, setting meetings, planning events, getting immediate feedback, has to be done from home.
Many people find that the biggest hurdle is not having access to physical components and prototypes to learn from and gain ideas from. Instead, learning methods have to shift from relying on physical interaction to instead relying on images and written information. Plus, getting all the same samples to every member of the team as development continues while they are working remotely is another hurdle to jump over. The need for complete and thorough communication becomes more and more necessary so that information learned can be accurately shared.
Overcoming Obtaining User Input
Like we mentioned at the beginning, additional planning was required for getting user input. Designing medical equipment requires contacting actual users in hospitals and asking them detailed questions about how the user interface layout should be. With the logistics and time constraints, there is the one significant flow of feedback that generally comes with projects like these. Especially when faced with a fast-paced situation like the global pandemic, where novice users need to be able to use and adjust the equipment as necessary, it’s crucial to get that feedback of how things should work. The interface should be intuitive and straightforward enough to make changes without constant expert supervision. Each ventilator should be designed in a way that can accommodate both senior and younger individuals.
Though there will always be disadvantages to having meetings over conference calls versus in-person, one benefit is that it leaves more time to collect more user input.
Bottom Line With COVID-19 Ventilator Design Lessons
When it comes to COVID-19 ventilator design lessons, the bottom line is that it’s essential to set boundaries on what you’re designing and make sure you put people in charge of ongoing requirements. Then, establish a line of constant communication between all involved team members so that all requirements are getting met. This is a good strategy for all projects, but mainly when working at a fast pace.
The project’s speed, especially when designing medical equipment during a global pandemic, really emphasizes the importance of adequately documenting design decisions. Important decisions impact the way the user interacts with the device quickly, and the reasons why those decisions get made should be noted. With proper documentation, group revisions are more manageable, and so are conclusions as to whether or not requirements are actually being met.
Outer Reef Technologies Develops Open Source Ventilator
At Outer Reef Technologies, we’ve developed an open-source ventilator that offers the same functionality and modes of FDA-approved ventilators on the market, and the “Omnis” ventilator design includes Assist Control Volume/Pressure Ventilation and CPAP. It’s made from six readily available components and can be constructed in less than an hour. We provide step-by-step instructions available along with a materials list, informational videos, a mobile patient monitoring app, and supporting firmware.
Our medical device engineering firm is ISO 13485 compliant. We named it Omnis from the Latin word for ‘everyone,” which is aligned with our goal to design and build an affordable and effective ventilator available to everyone across the world. Due to COVID-19, the need for more ventilators is overwhelming in the medical field. Mechanical ventilation is utilized in intensive and long-term care settings to help people suffering from respiratory failure. Other ventilators on the market cost up to $50,000 and are made from custom parts that can only be manufactured by a certain number of vendors. This means that it’s impossible to keep up with demand. That’s why Outer Reef stepped up to provide a better, more efficient, more affordable option to meet the needs of the medical market.
At Outer Reef Technologies, we provide engineering design solutions that include medical device development, robotics, firmware, electronics, software, mechanical design, QA/RA support, and manufacturing.
To learn more about our COVID-19 Ventilator, click here.
Leave a comment (all fields required)
Comments will be approved before showing up.