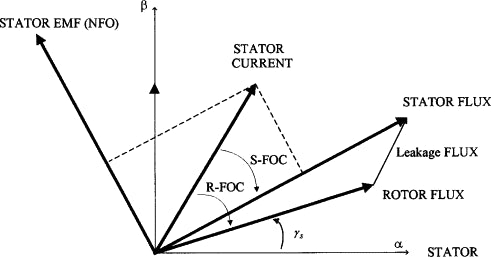
Motor controllers can come in many different configurations, but they all have one thing in common: Motor control is their primary function. Motor controller circuits regulate electric current to produce torque and rotational speed for BLDC motors. The most popular type of motor controller is field oriented control (FOC) which operates BLDC motors using a 3-phase sinusoidal field current to produce torque and rotational speed. FOC was originally designed for BLDC motors, but can be applied to other types of machines such as variable frequency drives or linear induction drives.
BLDC Motor
A BLDC motor (Brushless DC Motor) is a type of electric motor in which the individual magnetic poles are arranged around the armature (rotor) instead of being wound around the stator. BLDC motors can be controlled to rotate smoothly and with precise control, while maximizing efficiency and power density. BLDCs have replaced other types of motors in many applications including electric vehicles because they are more efficient than other types of motors.
The BLDC motor is a type of brushless DC electric motor mainly used for applications that require low weight and high precision. BLDC motors are widely used in home appliances, including dishwashers, fans, and clothes dryers. BLDC motors are also popular for use in industrial equipment such as electric vehicles (EV) and electric buses because they have fewer moving parts than other types of motors. BLDC motors are more efficient and powerful than permanent magnet synchronous motors or brushed DC motors because BLDCs use a 3-phase sinusoidal field current to produce torque and rotational speed. BLDCs have higher efficiency than all other motors, including synchronous BLDC motors. BLDCs are more expensive to manufacture because BLDCs require high-quality bearings, rotor and stator windings, and high-performance electronic controllers with advanced algorithms.
BLDC motors are difficult to control because they are asynchronous and the field current is rotating. This makes it challenging to supply power to the motor as needed. Traditional controllers, such as a PWM controller, can't compensate for an asynchronous motor, so use of BLDC motors requires a specific type of controller - one that can drive both AC and DC fields. Enter Field Oriented Control (FOC). FOC is designed specifically for BLDCs, and while not the only way of driving BLDCs, it is by far the most efficient.
BLDC Motor Controller
A BLDC motor controller is a motor controller that regulates the speed and torque of brushless DC (BLDC) motors. The abbreviation BLDC stands for "brushless, linear direct current". A BLDC motor controller is made up of components such as a switch mode power supply. They regulate voltage or current to the motor in order to control speed and torque.
A BLDC motor controller is designed by evaluating requirements for the application and choosing components that meet these requirements. They usually have multiple control loops, closed-loop feedback systems or computers which monitor speed and regulate this to control other factors of the motor.
A BLDC Motor Controller is composed of the following components:
- A low side power switch.
- A voltage regulator.
- Some type of controller for the power control loop.
- A sense element for feedback on motor current, if desired.
- Some type of power stage to step up low voltage signals or for high currents (usually this is a transformer).
- A sense element for feedback on motor voltage or current, if desired.
- Protection diodes and capacitors to protect components from transient voltages.
Regarding the design of a BLDC Motor Controller, you can choose which components meet your requirements such as their efficiency and weigh in when designing a new one!
How BLDC's Field Oriented Control Works
FOC is a control algorithm based on the mathematical processing of the stator flux linkages and speed/torque equations. A microprocessor processes the information in real time to synchronize stator currents with rotor position for each phase. The idea behind FOC is that an average current will create less torque ripple than a single current value for each phase.
Beginners might find it useful to understand how the flux linkages work in a BLDC motor when learning about FOC. Understanding how the flux works can help you realize why FOC is needed, and also give an idea of what's happening inside your controller when you change your power setting from high to low. Flux linkages are created by different windings of a BLDC motor. The flux produced from these windings generates a magnetic field that rotates with the rotor to produce torque in the stator when opposite ends of each phase is connected to an AC power source.
The equations for FOC are complex, so many "beginner" controllers simply use the three phases in a round-robin sequence that gives you an average flux linkage for each phase. As long as there's a balance of torque and current, this method works fine, but sometimes it doesn't give you consistent performance. The mathematical processing used in FOC is complex. A microprocessor processes rotor position, stator phase currents and flux linkages to adjust the current for each phase in real time. The result is a sinusoidal waveform that helps smooth out torque ripples while producing more consistent output power – especially at lower speeds.
The sinusoidal current waveform also gives you smoother motor operation, reducing noise and vibration by preventing "hunting" for the next operating point that's supposed to maintain a constant speed. With standard PWM for example, each phase is treated equally but the controller doesn't sense flux linkages. This causes undesirable current ripples and hunting because the rotor position isn't taken into account when processing power. FOC uses only one microprocessor terminal to control all three phases. The microprocessor is programmed to respond to rotor position by choosing the appropriate field current for each phase. This gives you an average stator current for each phase that produces more consistent power over time. The other terminals of the controller are used to monitor rotor position, adjust timing and calculate rotational speed.
As the stator is a "weak" field, each phase has to be energized with a current that's equal in magnitude for maximum torque. There's no way around this rule because the stator can't produce enough magnetic flux on its own to support BLDC operation. If you tried to use AC power with three different stator currents, the rotor would spin in circles and the motor wouldn't move at all. The microprocessor in your BLDC controller is programmed to use an average current to create torque and rotational motion. This is accomplished by checking the rotor position, calculating a new stator phase current based on this information and changing the settings for each phase. Three key variables are used by your controller to decide what field currents to set for each phase. These three variables are rotor position, total motor load and rotational speed.
Concluding Thoughts on Why FOC is the Preferred Control Algorithm
FOC is the preferred control algorithm because it can be applied to many industries. It's commonly used in motorized vehicles, but FOCs are also found in many other performance critical fields and medical applications. This type of BLDC controller may not work for all types of machines; however, if you're looking for a way to increase your efficiency without sacrificing power or performance, this should be one method that you consider implementing on your machine! If you have any questions about how Field Oriented Control could help improve your company's production process, let us know! Our team would love to chat with you more about our services and what we offer as well as answer any questions that might come up before making a decision. Give us a call at (954-323-7850) or visit us at www.outerreeftech.com
Leave a comment (all fields required)
Comments will be approved before showing up.