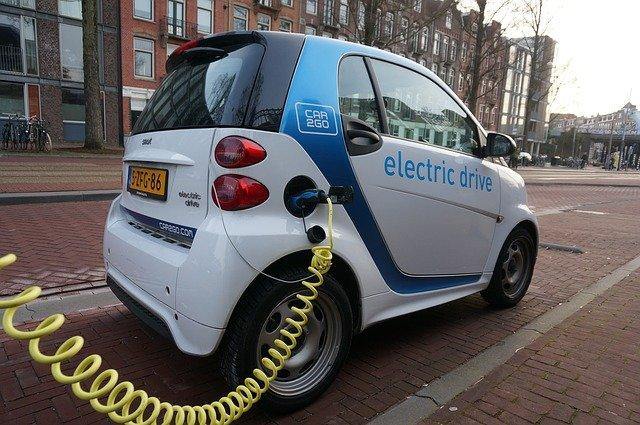
Brushless DC motors are a fantastic substitute for their predecessor, the brushed DC motor. As the name suggests, the Brushed motor uses commutators and brushes to control the motor's speed. Alternatively, the BLDC does not use brushes. It regulates the rotor's speed with specific drive signals that have been carefully designed to serve the purpose.
As compared to the brushed DC motors, BLDC has improved reliability, a longer lifespan, low weight, and small size. These motors have become increasingly popular lately. They find application in systems where efficiency is a crucial factor. BLDC motors are also known as high-performance motors since they can provide a large torque over a wide range of speeds. Click Here to find more information about high-quality BLDC motor controllers.
Speed Control Algorithms
Many different types of algorithms are used to control the speed and position of the sensorless BLDC motor.
A control algorithm must meet the following the three criteria
- PWM voltages should be generated to control the motor’s speed
- Must include a mechanism for motor commutation
- Must consist of a method to determine the rotor position using back emf.
Generally, the motor voltage is controlled with power transistors that operate as a linear voltage regulator. However, this fails to work in the case of high-power motors. Such motors use PWM control and require a microcontroller to provide speed control.
PWM is used to apply a variable voltage to the motor's windings. The voltage produced is directly proportional to the duty cycle of PWM. Upon proper commutation, its torque-speed characteristics become identical to that of a dc motor.
The power transistor’s commutation will energize the stator windings, leading to an optimum torque generation. In BLDC motors, the MCUs must be aware of the rotor’s position and undergo commutation within the stipulated period.
Sensorless BLDC Motors
The BLDC motors are generally of two types: Hall-Effect motors and Sensorless motors.
Hall-Effect BLDC motors can detect the motor's rotor's position with respect to its stator. In contrast, the sensorless BLDC motors do not use the Hall effect sensors to determine the rotor’s speed and position. Instead, they employ a phenomenon known as “back EMF.” Back emf is generated in the motor and controls the rotor’s speed and position.
The Working Of Sensorless BLDC Motors
In these motors, a voltage is applied across the motor's windings that causes the motor to rotate. The rotor’s movement through the motor's magnetic field leads to a voltage generation known as the back EMF.
According to Lenz’s Law, the back emf leads to a secondary magnetic field that acts against the magnetic flux responsible for driving the rotor. For any motor, the number of windings and magnetic flux is constant. However, the EMF produced is directly proportional to the rotor's angular speed. Thus, we can change the rotor's speed by changing the EMF value generated.
Field Oriented Control Of Sensorless BLDC Electric Motor And Controller
Field oriented control is a popular method for variable frequency control of stator. It is used to control the torque of three-phase electric motors. With the help of FOC, you can independently control the flux and the torque. This method also offers a rapid dynamic response which is required by several electrical appliances such as washing machines. Also, FOC does not produce torque ripples and greatly improves efficiency.
Proportional Integral Controllers are used in this method instead of Pulse Width Modulation. As a result, electric motors operate smoothly over the full speed range and generate maximum torque at zero speed. Moreover, this method helps control both high and low speeds of the motor.
Another advantage of using FOC is that it delivers more accurate control in the high-performance motors by providing fast acceleration and deceleration.
Field-oriented control finds application in pumps, fans, conveyors, etc. It is mainly used in industries where long-term reliability is needed.
Conclusion
Sensorless BLDC motors offer significant benefits over the Hall-Effect DC motors. The sensorless motors provide reduced costs and require fewer interconnections between the motor and the drive module. However, they are complex to design. The Hall-Effect motors in some instances find an edge over the sensorless motors for low-speed applications.
Leave a comment (all fields required)
Comments will be approved before showing up.