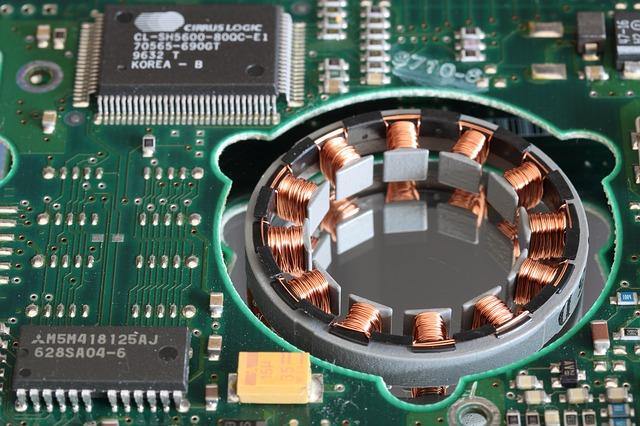
The brushless DC motor, also known as the BLDC motor, has become increasingly popular in various industries, including automotive, HVAC, and even the medical field. It eliminates the need for mechanical commutators used in traditional motors. It replaces them with an electronic device that improves both the reliability and durability of the unit it is operating in.
Another benefit of BLDC motor controllersis that it can be made smaller and lighter than others while still delivering the same power output. This is ideal for applications where space is a little tight. However, even with the clear advantages, the downside is that BLDC motors do need electronic management to run. A microcontroller that uses input from sensors indicates the rotor’s position and is required in order to energize the coils at just the right moment. The precise timing will allow for accurate torque control and correct speed and ensure the motor runs at peak efficiency.
This article will explain some of BLDC motor operation fundamentals and the advantages and disadvantages that come with them.
Motor Controllers For Product Development and Medical Equipment
Let’s dive into some of the functionalities of brushless motor controllers and how it might be useful in developing medical equipment.
How a Brushless DC Motor Works
First, we’ll try to describe how a brushless DC motor works. A BLDC motor is a permanent magnet synchronous motor with a unique back-EMF waveform, which allows it to behave in a similar fashion to a Brush DC (BDC) motor. Some people often get confused with these motors’ name, as BDC motors do not directly operate using a DC voltage source. You can think of a BLCD motor as a DC motor turned inside out, as the basic principle of operation is like that of a DC motor.
BLDC motors have rotors with permanent magnets and a stator with windings. Both the brushes and the commutator have been removed, and the windings are connected to the control electronics. These control electronics replace the commutator and energize the windings in a rotator pattern around the stator. The energized stator winding leads the rotor magnet and switches just as the rotor aligns with the stator.
Controlling a BLDC motor
When it comes to Brushless DC motors, magnetic fields are generated by magnets mounted right on the rotor and coils in the stator. The stator windings usually come in a 3-phase configuration and are around to be 120 electrical degrees apart. The sum of the force generated by these three phases is what will cause useable motor rotation.
Though it depends on how the individual coils are driven, they can either interact to create force that doesn’t generate rotational torque, or they can produce energy that does generate a rotation. These are known as quadrature and direct force. Quadrature forces run perpendicular to the rotor’s pole axis, and the non-torque producing direct forces run parallel to the rotor’s pole axis.
When you want to generate rotation, you want to maximize quadrature while minimizing direct torque generation. If your rotor angle is measured using back EMF, position encoder, or a Hall sensor, then you’ll know the direction of the magnetic field from the rotor.
Bottom Line
We think that BLDC motors offer several advantages over conventional motor controllers. First, it eliminates the mechanical part of the motor that reduces efficiency, wears out, and can fail catastrophically. Because of the development of powerful magnets, BLDC motors’ production can produce the same power as brush type motors while fitting into much smaller spaces.
As we mentioned, one perceived disadvantage is that BLDC motors, unlike the brush type, need an electronic system to supervise the energizing sequence of coils and provide control functions in other areas. The motors cannot operate without these electronics. However, since the increase in popularity of these robust electronic devices, designing a circuit has become relatively inexpensive and straightforward. A BLDC motor can even be set up to run in a basic configuration without even using a microcontroller when you employ a modest three-phase sine or square-wave generator. Utilizing an 8-bit microcontroller, which is programmed with factory-supplied code or the developer’s own software, is relatively inexpensive to the control system. However, it offers the user much greater control over the motor to ensure that it runs on optimum efficiency while still offering precise speed or torque-output.
When You Need The Best, Outer Reef Can Help
At Outer Reef Technologies, we help many people develop a wide variety of motor controller solutions for medical applications and other developing products. Outer Reef would love to help you find a solution for your specific application requirements, from simple mobility solutions to more sophisticated medical equipment like ventilators and surgical robots.
We specialize in medical equipment and product development, so we know that there are vital factors that need to happen when it comes to the medical field. Things like compact size, precision, quiet operation, easy usability, and efficiency are all at the forefront of our strategy. With our high-torque density brushless motors, precision drives, and more that are designed to exceed expectations, we are confident we can find a unique, customized solution to meet your medical equipment needs.
Leave a comment (all fields required)
Comments will be approved before showing up.