Managing the Design and Development of Medical Devices as per ISO 13485 Quality Management System (QMS)
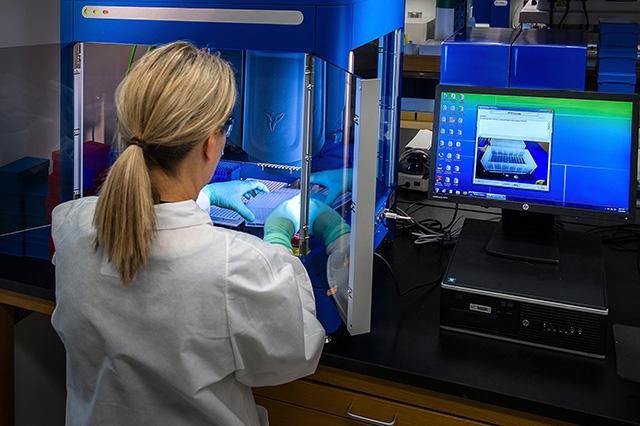
ISO 13485:2016 defines requisites of the Quality Management System for the design and manufacture of Medical Devices. When an organization is ISO 13485 certified, it means that the organization has successfully implemented the Quality Management System defined by ISO 13485. The certification evaluates whether the Quality Management System is effective and appropriate. It emphasizes on the efficacy and safety of all medical devices produced by that particular organization.
Although different countries have their set of ordinances when it comes to the standard of quality management, ISO 13485 is the primary management system in all the countries. The current version is 13485:2016. This global standard is mandatory in some countries.
The design and development phase of medical devices is not the same as other manufacturing processes. The process of manufacturing medical devices has to deal with product safety, regulations, specific requirements, end consumer needs, etc. The criticality of the entire design and development phase is that, if the manufactured device fails to meet certain regulations, it will not reach the market.
Requirements of Medical Product Design and Development
-
Procedure: The organization needs to document the logical phases of medical device development. The entire procedure should be structured.
-
Planning: One of the key phases of medical device development is adequateplanning. It helps to eliminate unnecessary delays. In this phase, objectives are defined. The organization also breaks down major activities. In short, it defines the timeline of every activity involved in the project.
-
Inputs: The quality of inputs is crucial to producing the right outputs. There are a few things that the organization must include as their inputs. Some of them include consumer and end-user requirements, intended application, usability requirements, sterilization requirements and service needs, ergonomics and safety factors, economic study and costing feasibility, etc.
-
Outputs: Design Outputs are produced by the organization in several different formslike environmental specifications and manufacturing process. Parts, raw materials, finished device specifications, design history file to demonstrate that the design was validated and verified, product identification, packaging, traceability, manufacturing, etc.
-
Review: Reviewing the design of a medical device is a detailed step that addressesseveral customers and manufacturing concerns. For instance, the organization will have to demonstrate that their design successfully meets the requirements of a product. It will also have to ascertain that the design of their device is compatible with processing capabilities, all safety concerns are addressed, the service components are adequate, etc. The design generally is reviewed in a meeting.
-
Verification: Design verification is a crucial step in the process of medical device product development. Medical product design companies verify the quality of products with the help of tests, substitute calculations, inspection, review of documents like drawings, specifications, plans, procedures, etc.
-
Validation: Validation of the device is done after its verification. This phase makes sure that the device is developed as per the requirements of end-users. Initially produced samples are validated and their actual performance is assured. Records of the validation process should be maintained.
-
Transfer: The entire procedure of transferring the design to medical product development is documented by the organization. It is not referred to just handingover the design to the manufacturing department, but it means that the development of the medical product is possible and that the design can be successfully transferred.
-
Control of Changes: A change in the design can be needed at any point in time based on several phases carried out by the medical device development companies. Before enforcing any changes, it is crucial to verify, document, approve, and validate the changes before implementing them.
Conclusion
ISO 13485:2016 has made medical product development safe for organizations. The design and manufacturing process is critically reviewed at each step to address all possible shortcomings. It helps them correct the design and development flaws and eventually incorporate improvements in the device manufactured.
Leave a comment (all fields required)
Comments will be approved before showing up.